Exactly How Reliable Welding Evaluation Enhances Structural Honesty and Longevity
In the realm of construction and design, the relevance of welding examination can not be overemphasized, as it plays a crucial function in guaranteeing structural honesty and expanding the lifespan of jobs. Sign up with the exploration of just how reliable welding inspections can transform potential vulnerabilities into toughness, contributing to the long-lasting success of buildings.
Value of Welding Evaluation
Ensuring the architectural honesty and security of bonded buildings mandates extensive welding examination procedures. Welding evaluation offers as an essential protect in the building and manufacturing industries, where the strength and longevity of joints dramatically influence the overall performance of frameworks.
Along with security, welding inspection plays an important function in quality control. By sticking to established requirements, examinations identify the consistency of welds, guaranteeing that each meets the desired stamina and visual demands. This uniformity is vital not only for safety and security yet likewise for preserving the credibility and reliability of producers and fabricators. In addition, governing compliance is a considerable vehicle driver of welding examination practices. Sector criteria and codes, such as those from the American Welding Culture (AWS) or the International Company for Standardization (ISO), demand adherence to stringent standards, highlighting the significance of examinations in satisfying these specialist and lawful obligations.
Secret Inspection Methods

Ultrasonic Testing (UT) utilizes high-frequency audio waves to find subsurface flaws, providing precise details regarding weld honesty without causing any kind of damage. Radiographic Evaluating (RT), including X-rays or gamma rays, supplies a detailed photo of the weld's internal framework, disclosing concealed flaws. Magnetic Particle Checking (MPT) is one more non-destructive technique, specifically effective for discovering surface area and near-surface gaps in ferromagnetic products.
Penetrant Testing (PT) entails the application of a liquid color to expose surface-breaking defects, providing a straightforward and economical service for non-porous products. Each technique has its certain applications, strengths, and limitations, and typically a combination of methods is employed to attain extensive examination results. Mastery of these strategies boosts the reliability and toughness of bonded structures, straightening with safety and security and performance expectations.
Identifying Common Problems
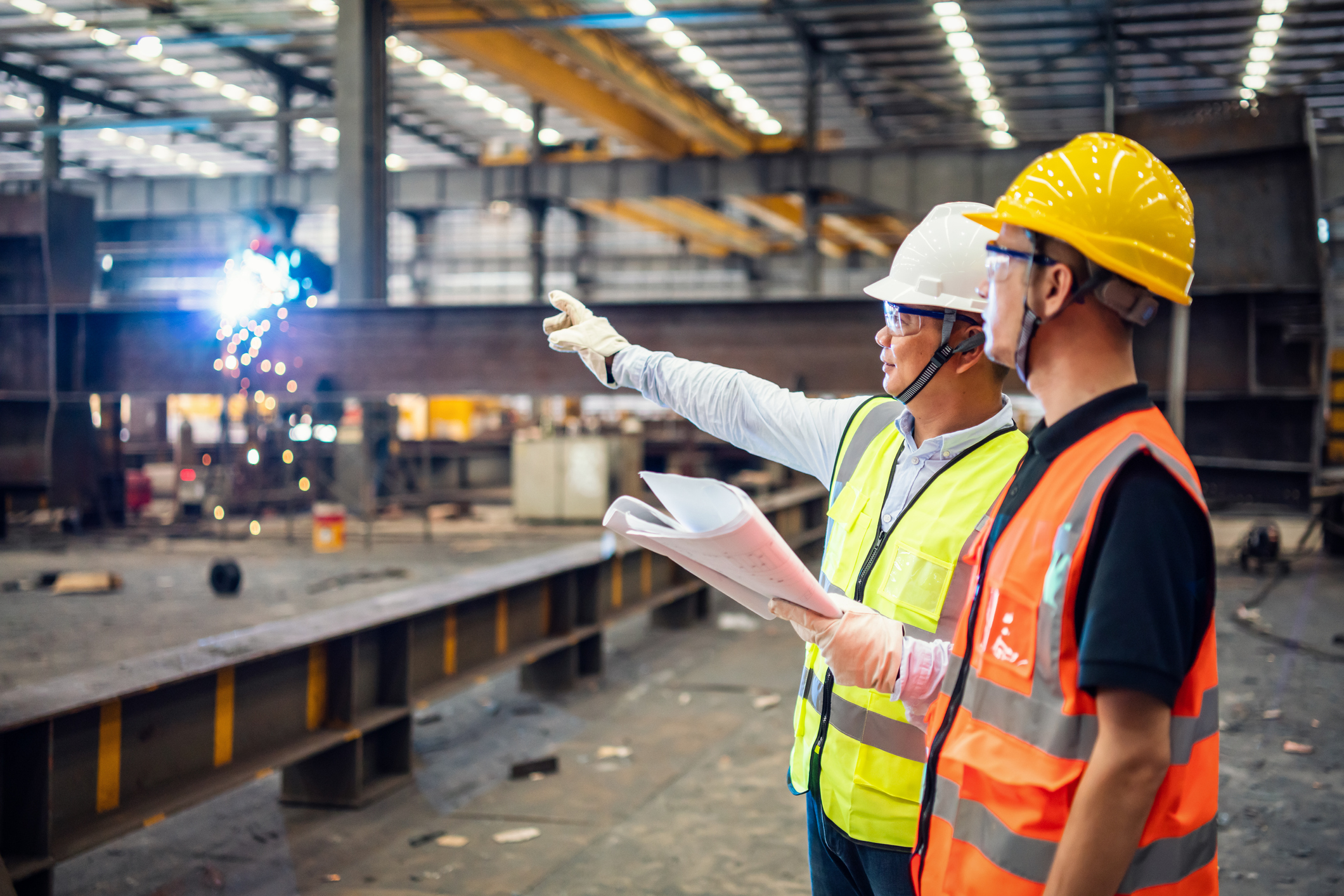
Porosity, identified by gas pockets within the weld, lowers the weld's strength and resilience. Fractures, which can take place during or after welding, position substantial risks due to their possible to circulate under stress and anxiety.
Incomplete combination, where the weld metal stops working to bond entirely with the base product, weakens the architectural integrity, leading to weak joints. Slag inclusions take place when non-metallic products are trapped in the weld, compromising its strength and high quality.
Identifying these problems through meticulous inspection techniques, such as visual examination, ultrasonic testing, or radiography, is crucial. Dealing with these worries makes certain weld high quality, eventually supporting the structural stability and safety and security of the constructed setting.
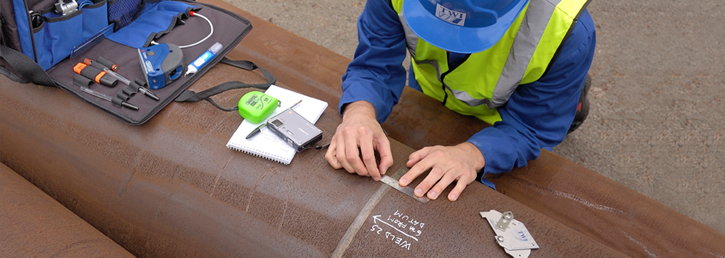
Enhancing Architectural Performance
Comprehending the value of determining common weld defects normally brings about checking out techniques for boosting structural performance. The foundational method for improving performance requires employing innovative welding techniques and products that mitigate defect incident. Making use of top notch filler materials and guaranteeing proper heat control can significantly minimize concerns such as porosity and breaking, thereby improving the weld's honesty.
Integrating state-of-the-art welding modern technologies, such as laser welding and rubbing mix welding, more amplifies architectural resilience. These strategies offer remarkable accuracy and Go Here lowered thermal distortion, directly impacting the longevity and stamina of the welded frameworks. Taking on automated welding systems can make certain repeatable and constant weld quality, minimizing human error.
In addition, implementing strenuous pre-weld and post-weld treatments is important. Correct joint style, surface area preparation, and stress-relieving processes add to optimal weld performance. Carrying out comprehensive pre-weld examinations enables early discovery of prospective problems, facilitating prompt corrections prior to they jeopardize the framework.
Long-term Advantages of Examination

Via cautious examination methods, the long-lasting advantages to architectural honesty ended up being significantly apparent. Consistent and comprehensive welding examinations play a critical duty in avoiding architectural failings by determining problems and incongruities early in the building process.
Moreover, regular inspections add to preserving compliance with industry criteria and guidelines, consequently avoiding monetary and legal repercussions. This adherence to high quality assurance not only improves the dependability of the framework yet additionally fosters depend on amongst stakeholders, including customers, designers, and regulatory bodies. The thorough documentation of examination outcomes functions as a beneficial source for future maintenance and repair service initiatives, facilitating educated decision-making.
On top of that, reliable evaluation techniques sustain technology by integrating innovative technologies such as non-destructive screening and digital imaging, which can boost accuracy and efficiency. This technological combination further underscores the commitment to excellence in structural stability. Inevitably, buying careful welding evaluations is a prudent strategy that generates considerable long-term benefits, protecting both the physical and economic investment in infrastructure jobs.
Verdict
Efficient welding evaluation plays an essential function in improving structural integrity and durability by recognizing flaws early in the building and construction process. Making use of techniques such as visual evaluation, ultrasonic testing, and radiographic testing guarantees the discovery of problems like fractures and porosity that jeopardize weld stamina. Strenuous inspections ensure conformity with industry requirements, thus lengthening the life expectancy of structures, lessening costly fixings, and cultivating stakeholder trust fund in the reliability and safety of bonded building and constructions.
In the world of building and engineering, the importance of welding evaluation can not be overemphasized, as it plays a crucial duty in making certain structural honesty and extending the lifespan of jobs.Ensuring the structural honesty and security of bonded building and constructions mandates rigorous welding examination procedures.Structure upon the value of welding inspection in securing structural integrity, recognizing the vital examination methods comes to be critical for reliable implementation. Reliable welding evaluation encompasses a range of visit here methods created to evaluate weld high quality, making sure conformity with stringent engineering standards - Welding Inspection Madison.Reliable welding examination plays an important function in improving architectural honesty and longevity by identifying flaws early in the construction official site procedure
Comments on “The Function of Modern Technology in Modern Welding Inspection Madison Practices”